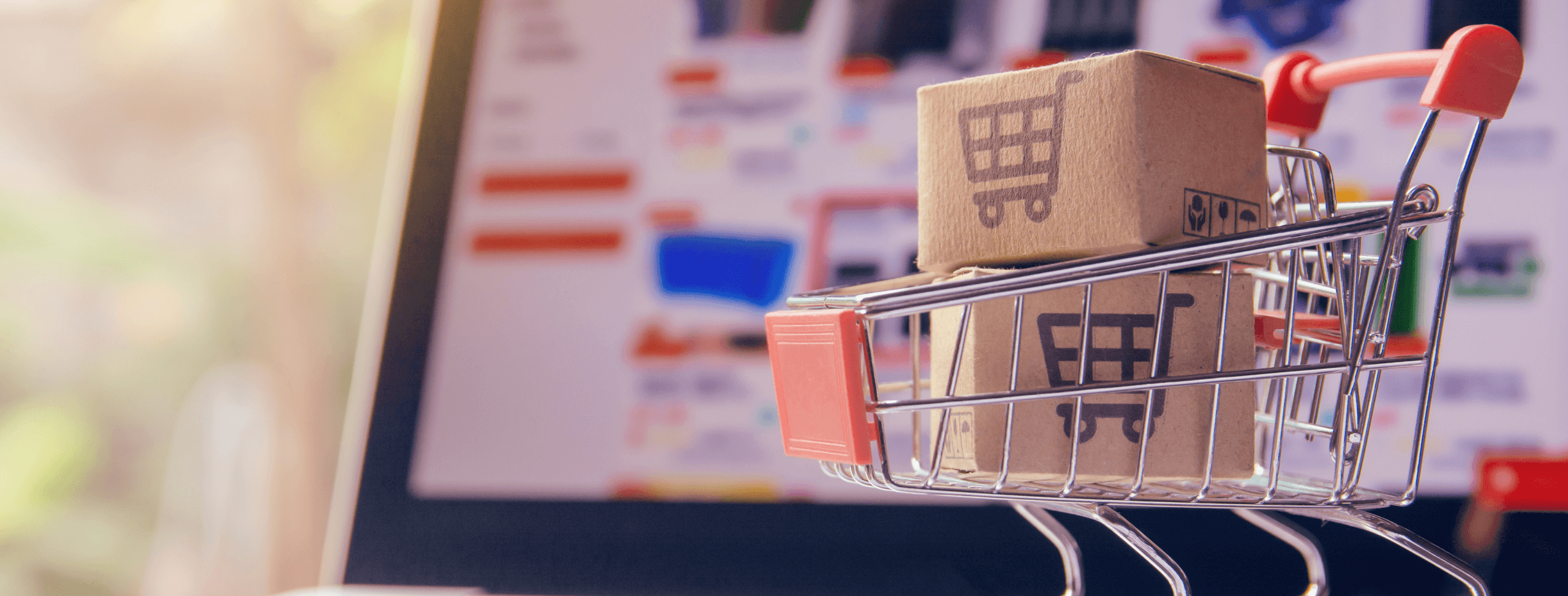
Although it seems like a simple concept, the different types of warehouses to choose from could be more of a business essential than you think. The type of warehousing that’s right for you depends on your specific industry, location, and requirements. One crucial decision-making process involves choosing between private or public warehousing. Private warehouses are owned by companies for exclusive use, while public warehouses, or third-party logistics (3PL) providers, offer shared storage solutions for multiple businesses. Each option has its advantages and disadvantages, and the choice depends on factors like size, budget, and future scalability. There is a specific option for every business.
HERE AT BRAY SOLUTIONS, WE HAVE BROKEN DOWN THE MOST COMMON, YET DIFFERENT, TYPES OF WAREHOUSES:
A private warehouse is a storage facility owned and managed by a single company for its exclusive use. Unlike public warehouses, which serve multiple clients, private warehouses provide complete control over storage and distribution processes. This allows companies to tailor their logistics operations to meet specific needs, ensuring optimal efficiency and effectiveness.
Private warehouses are a crucial component of supply chain management, offering solutions to various supply chain constraints, irregular consumer behaviour, and overall economic conditions. By owning and managing their storage facility, companies can better align their warehousing strategies with their business goals, enhancing overall supply performance.
Private warehousing offers several advantages, including:
Private warehousing also comes with several challenges, including:
Private warehouses play an important role in the distribution chain, offering dedicated storage for materials and proper inventory management. By having control over their own private warehouse, companies can streamline their storage and shipping processes, reducing transportation costs and improving customer satisfaction. Effective management of a private warehouse enables companies to manage the workflow of logistics, minimise time, and increase order fulfilment rates. This control over warehousing operations allows businesses to respond quickly to market demands, ensuring that products are available when and where they are needed, ultimately enhancing overall supply efficiency.
Public warehouses have the option to allow companies with short-term needs to lease them. It is ideal for retailers with their own private warehouse but needs additional storage, perhaps in seasonal peaks. Once busy periods end, they can go back to normal without a contract keeping them tied in.
When considering public and private warehousing, it’s important to weigh the benefits and limitations of each type to determine the best fit for your business needs.
Whilst Bray offer it all from picking and packing to distribution. Distribution centres are warehouses where storing products is a temporary occurrence. These storage facilities serve different purposes, with private warehouses owned by individual companies and public warehousing operated by third-parties to manage inventory for multiple businesses. In addition to distribution centres, cold storage warehouses are specialised facilities designed to preserve perishable goods such as food, pharmaceuticals, and chemicals. Distribution centres are a point in the supply chain where products are almost instantly shipped out on arrival. They are usually used for the shipping of perishables to prevent spoiling in storage. A distribution centre will usually receive shipments in the morning and distribute them by the end of the same day.
Fulfilment centres are specialised privately owned warehouses designed to cater to the needs of e-commerce businesses. These centres excel in efficiently processing and fulfilling customer orders, ensuring that products are stored, packaged, and shipped with precision. By leveraging a privately owned warehouse, e-commerce businesses can benefit from significant operational and financial advantages, including control and customisation opportunities for supply chain management. The initial costs involved in establishing such a facility can be offset by long-term cost savings and the potential to generate revenue by renting out excess space.
Fulfilment centres offer a comprehensive range of services, including inventory management, order processing, packaging, and shipping. This makes them particularly valuable for businesses with high order volumes or those requiring specialised handling and packaging. Additionally, fulfilment centres often provide returns processing and detailed inventory reporting, further enhancing supply chain management. By outsourcing these operations, businesses can improve customer satisfaction, reduce operational costs, and gain a competitive edge in the market.
Private warehouses are just that – private. They are privately owned, usually by big retailers to store their extra inventory in bulk, especially during busy seasons, offering various advantages of private warehousing such as efficient inventory management and enhanced security features. Public and private warehouses have key differences in their functions and benefits. Strategically positioned public and private warehouses can reduce transportation costs by bringing products closer to consumers. Private warehousing requires big investments from the owner, but they most likely prove to be very cost-effective in the long run due to significant cost savings. Implementing advanced inventory management systems in private warehouses can further enhance operational efficiency and data tracking.
AUTOMATION IN THE WAREHOUSE
Automation is the new method, with such advanced technology at our fingertips. Worldwide sales of warehouse automation technology, such as robotics or logistics, reached $1.9 billion in 2016. In addition, they are expected to reach a market value of $22.4 billion by the end of 2021.
Automated warehouses require very little human interaction. Automated warehouses operate using the latest technology and carriers to carry out day-to-day warehouse operations without much help from us humans.
Automated warehouses represent the pinnacle of modern warehousing, utilising advanced technology and robotics to optimise storage and retrieval operations. These private warehouses are designed to maximise efficiency, reduce labor costs, and enhance accuracy. Key features of automated warehouses include automated storage and retrieval systems (AS/RS), conveyor systems, and sophisticated warehouse management systems (WMS) that streamline inventory control and warehouse operations.
The advantages of automated warehouses are manifold. They significantly boost productivity, lower labor expenses, and improve accuracy in inventory management. Real-time inventory tracking and reporting capabilities enable businesses to make informed decisions about their supply chain, enhancing overall efficiency. Moreover, automated warehouses contribute to sustainability by minimising energy consumption and waste.
However, the implementation of automated warehouses requires a substantial upfront investment in technology and infrastructure. Businesses must carefully assess their needs and resources before adopting this approach. For those with high-volume storage and retrieval requirements, automated warehouses offer a competitive advantage, driving efficiency and effectiveness in supply chain management.
The cold chain is a supply chain that supports and organises the storage and transportation of temperature-based food goods. Effective storage and distribution processes are crucial in maintaining the quality and safety of temperature-sensitive goods throughout the cold chain. A cold chain will help extend the shelf life of many perishables such as frozen food, pharmaceuticals and seafood.
If the world had a properly functioning cold chain, it is predicted that perishable food loss could be brought down to just 2%. (*) The cold chain is growing even faster than the world’s economy and the logistics industry as a whole. This is because of the increasing need for systematic storage systems of perishables, pharmaceuticals and chemicals to prevent waste or spoilage.
The ever-advancing technology in warehouse development is making cold chain more affordable and attainable. As consumers buy more fresh and frozen food, the demand for more cold chain capacity grows. They are also becoming more interested in supply chains, demanding a transparent, clean, ethical supply chain.
So, there are different types of warehouses to suit a wide range of business needs. This could be to suit your industry, your products or even your availability of personnel. Pick the right option for you and your business processes will run more smoothly and streamlined for company success.
Private warehouse management involves several key aspects, including:
By focusing on these key aspects, companies can ensure that their private warehouse operations are efficient, cost-effective, and aligned with their overall business objectives.
Need any further advice on warehousing and storage? Reach out to Bray Solutions for the perfect 3PL Solution.
We integrate with a number of different systems.
Get in touch to find out how we can help.