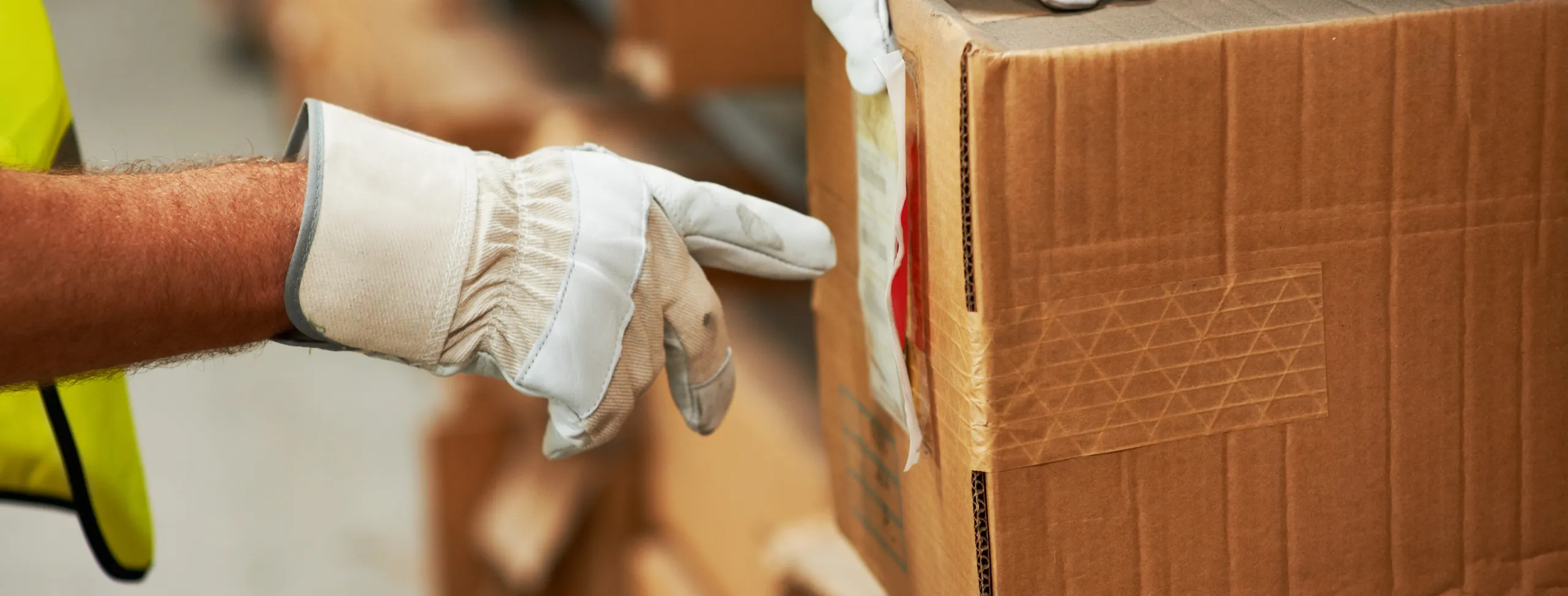
Last year, the Health & Safety Executive (HSE) revealed that 621,000 non-fatal workplace injuries occur in Britain each year. Whilst it hasn’t led to fatal damage on those occasions, that is still 621,000 too many.
To reduce the risk of warehouse hazards, you must ensure you have a plan in place to prevent them from happening. Safety measures are critical; they will protect employees from injury or even worse, death. Then, in turn, it will protect the business from liability and lawsuits.
Having a warehouse safety checklist is essential if you want to prevent risks safely and efficiently.
In this blog, we discuss potential warehouse hazards and prevention solutions.
It’s a common occurrence that a significant amount of space in warehouses is dedicated to pallet storage. Ensuring that all pallets are appropriately stored, and racking is kept in top form is vital as overloading them with products can damage both the pallets and products stored on them.
Limit how much stock you pile onto pallets, a smaller weight pressure will prevent pallets from collapsing. Also, only use high-quality, intact pallets that show no apparent or serious signs of deformities and no major breaks.
Even something as small as a scratch on racking can prove dangerous if not repaired or replaced. Any damage, including dents, will debilitate the racking system and could encourage sections to collapse.
Racking guards, such as bollard posts or aisle protection beams can protect the rack from collapse.
Sorting areas often operate using a conveyor belt to organise products into their labelled shipping area. When correctly safeguarded, a sorting conveyor is an adequately safe piece of equipment; however, if mandatory safety regulations are not in place, there is a risk that terrible injuries can happen.
To ensure conveyors remain a safe tool to use, sorting areas must have guards surrounding moving parts, including belts, gears and motors. You can also use rails to help prevent products from falling over the edge of a conveyor, limiting damage to products and the risk of staff tripping.
All sorting operators and maintenance staff should practice proper training on conveyor safety, including how to operate, maintain, and shut down the system when needed.
To prevent warehouse hazards, having enough space is essential. A warehouse could ultimately have to find space for boxes, forklifts and other warehouse machinery, scrap materials, pallets and of course space for staff to navigate throughout. Less space means more chance for vehicle crashes and employee trips.
One answer is floor tape. We know what you’re thinking. How could something as simple as floor tape solve all of your warehouse space issues? Although it isn’t considered a must-have safety solution, using it to carve out different areas will begin the process of keeping everything in order. Rails will also act as a barrier to storage and staff.
Check out our previous blog on making the most of your warehouse space here.
Make sure everyone in the warehouse has had the appropriate training for their role. For example, have all your warehouse staff learnt how to lift items correctly? Or attended forklift driver training? This type of training is necessary to limit warehouse hazards and can go a long way in preventing accidents when the warehouse is a little busier than usual. With products, boxes, and people filling the warehouse floor, an unskilled staff member with no training can easily cause danger.
Although warehouse hazards are common, they are easily avoidable with the correct procedures in place. There is so much to consider when running a warehouse and Bray Solutions can help with full 3PL fulfilment if you’re feeling overwhelmed.
We integrate with a number of different systems.
Get in touch to find out how we can help.