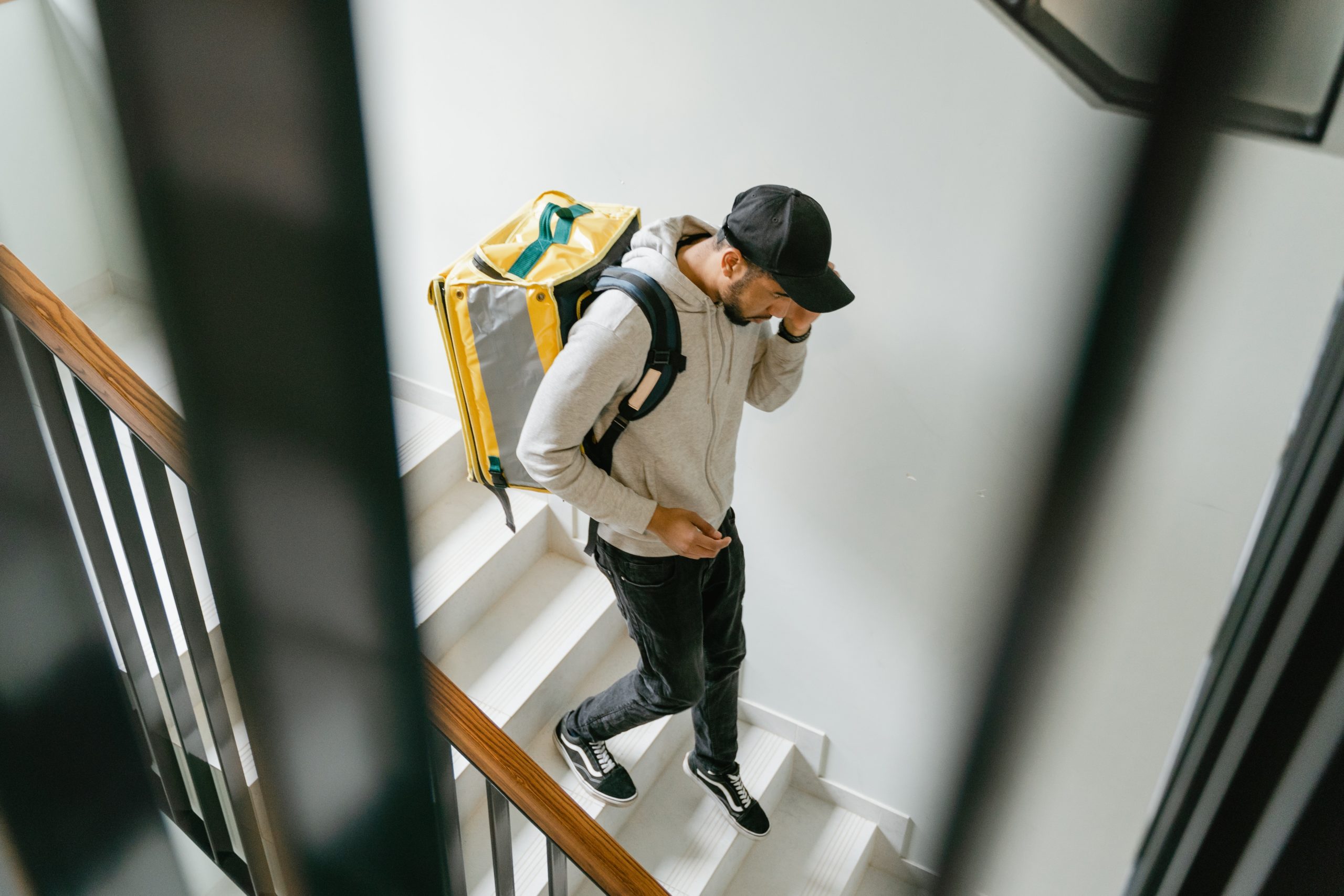
Quality control is a critical aspect of contract packing, ensuring that products meet the highest standards of safety, functionality, and customer satisfaction. The mark of a good co-packer is their commitment to quality control.
This is a process used to ensure that a product or service meets specified standards of quality. It involves systematic inspection, measurement, and testing of products to identify defects or deviations from the desired quality. The goal is to maintain consistency, reliability, and safety in products by detecting and addressing issues early in the production process. This process helps prevent faulty products from reaching customers, thereby ensuring customer satisfaction and adherence to regulatory requirements.
Maintaining brand reputation is a crucial aspect of any business, and one of the key elements in achieving this is through consistent and reliable product packaging. Customers expect high-quality packaging that reflects the product inside, and any deviation from this expectation can lead to dissatisfaction and harm the brand’s image. Here’s a look at why ensuring consistency and reliability in contract packing is vital for maintaining brand reputation.
Customers develop trust in a brand when they receive products that are consistently well-packaged. High-quality, uniform packaging reassures customers about the reliability and quality of the product. Consistency signals professionalism and attention to detail, reinforcing the brand’s commitment to quality.
Packaging is often the first physical touchpoint a customer has with a product. If the packaging is substandard, it can create a negative perception of the product itself, regardless of its actual quality. Conversely, high-quality packaging can enhance the perceived value of the product.
In the luxury market, packaging plays a significant role in the overall customer experience. For instance, luxury beauty brands invest heavily in elegant, sophisticated packaging to align with their brand image. Any inconsistency in this aspect can detract from the customer’s perception of the brand’s value and prestige.
Reliable packaging ensures that products are protected during transit and storage. This is particularly important for delicate items or products that have strict regulatory requirements, such as pharmaceuticals or food items. Reliable packaging prevents damage, contamination, and spoilage, ensuring that customers receive the product in perfect condition.
Inconsistent or unreliable packaging can lead to product damage, incorrect labelling, or other issues that result in customer complaints and returns. This not only affects customer satisfaction but also increases operational costs. Ensuring reliability in packaging helps minimise these risks, leading to higher customer satisfaction and loyalty.
Implementing rigorous quality checks at every stage of the packing process is essential. This includes inspecting incoming materials, monitoring the packing process, and conducting final inspections before dispatch. Quality control ensures that any defects or inconsistencies are caught and rectified before the product reaches the customer.
Training employees and standardising procedures are critical for maintaining consistency. Clear guidelines and regular training ensure that everyone involved in the packing process understands and adheres to the required standards.
Automated systems reduce the risk of human error and ensure precision in packing processes. Technology also allows for better tracking and monitoring of the packing process, providing insights for continuous improvement.
Outsourcing packing, or contract packing, offers several significant advantages for businesses.
Example: A contract packer with experience in the pharmaceutical industry will be well-versed in regulatory compliance, ensuring your products are packaged safely and legally.
Operational Cost Savings: Outsourcing also reduces the costs associated with hiring, training, and retaining a packing workforce. Contract packers manage their own labour force, saving you recruitment and training expenses. In this case, a small beverage company can save significantly by outsourcing its bottling and labelling processes, allowing it to focus on product innovation and market expansion.
Customisation: They offer flexible packing solutions tailored to your specific requirements, whether it’s for a limited-edition product or a large-scale production run. For example, a toy manufacturer can quickly scale up production during the holiday season without the need to invest in additional equipment or workforce.
Ensuring consistency and reliability in contract packing is essential for maintaining brand reputation. High-quality, uniform packing builds customer trust, reflects product quality, and reduces operational issues like returns and complaints. Partnering with a trusted contract packer like Bray Solutions ensures that your products are packed to the highest standards, supporting your brand’s reputation and success.
We integrate with a number of different systems.
Get in touch to find out how we can help.