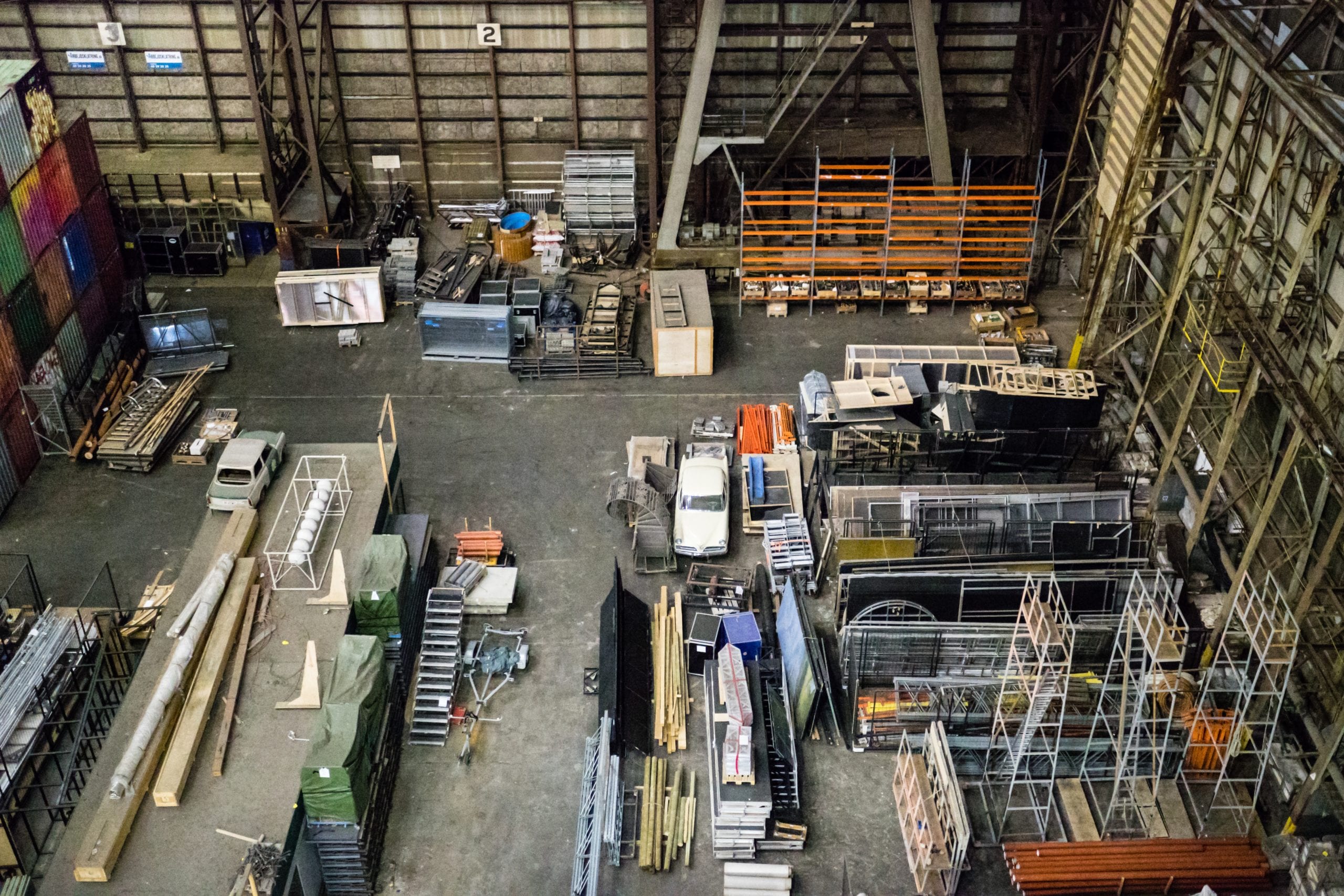
Picking and packing is essentially the heart of any Warehouse operation. Especially considering it accounts for 45% of the total operating costs. It is the process of selecting the correct products and packaging them up for delivery to the customer (or retail store).
The reason it is so important is that how efficiently a warehouse and company can deliver its products highly affects customer satisfaction rates, and impacts a business’s bottom line.
When choosing a 3PL, there are steps to the pick and pack process worth learning more about. Below we explore the process here at Bray Solutions, and why the right level of trust in your chosen 3PL is essential.
Step 1: Processing
Orders are processed daily by Bray Solutions Sales Administrators via the Warehousing Management System (WMS), then printed and passed over to the warehouse team.
Customers then have two options to move forward, they can either have their orders integrated, which means their orders drop straight into the WMS system and the in-house team will process them. Or if a customer prefers it, they can send over orders to the team via email (or in a spreadsheet) to be manually processed.
Step 2: Information Retrieval
A member of the Brays team will scan the pick ticket with a handheld scanner, which will show the order on the screen. After scanning the pick ticket, they will then scan a pick bin which is assigned to this order. This makes it easier for the packing team to double-check the items before packing.
These steps may seem over the top, but they are all parts of the process which ensures the right product makes its way to the customer as quickly as possible.
Finally, the automated voice on the scanner informs the picker of the product’s location, stock keeping unit and the quantity on the order. Prompting the picker to make their way to the location.
Step 3: Product Selection
On arrival at the location, the picker will scan the location barcode and then the barcode on the product itself. Both of these scans ensure the picker has got the right location and product. They will then manually input the quantity into the scanner and confirm. They then place the item into a pick bin ready to be packaged by the packing team.
Only when the correct barcode has been scanned will the automated voice instruct the picker onto the next stage. The scanner does not allow the team to move on to the next item/order if the team scans the incorrect barcode. This once again reduces the margin of human error and ensures the quality of Brays Solution services.
Step 4: Packing
Once completed, the picker will take the order back to the packing station, where a packer will scan the pick bin to bring up the order. This is so they can physically check the order is 100% correct.
With the confirmation of its accuracy, the item is then either placed into either a mailing bag or a box. Customers at this point can either provide their own packaging or instruct Bray to use extra packaging for certain products. We endeavour to match the requests of all our customers.
Step 5: Final Processing
With the order now securely packaged, a member of the Brays team will process the label through the Warehouse Management System. Completing the cycle. The courier service will have already been assigned by the customer when the order was first processed. Various integration options are available at Bray Solutions, just get in touch.
The label is then attached to the bag or box, and the order is placed in either a cage for smaller products (usually being sent via Royal Mail), a pallet for larger items or a magnum.
Step 6: Sending
Finally, these are loaded onto the desired courier once they have arrived for their daily collection. We ship daily to ensure packages arrive as promptly as possible, and ship orders out the same day to match demand.
Here at Bray, we know how important the picking and packing process is to our clients, and work hard to ensure our level of accuracy is as high as possible. Get in touch with us to discuss how we can ensure your customer’s satisfaction.
We integrate with a number of different systems.
Get in touch to find out how we can help.