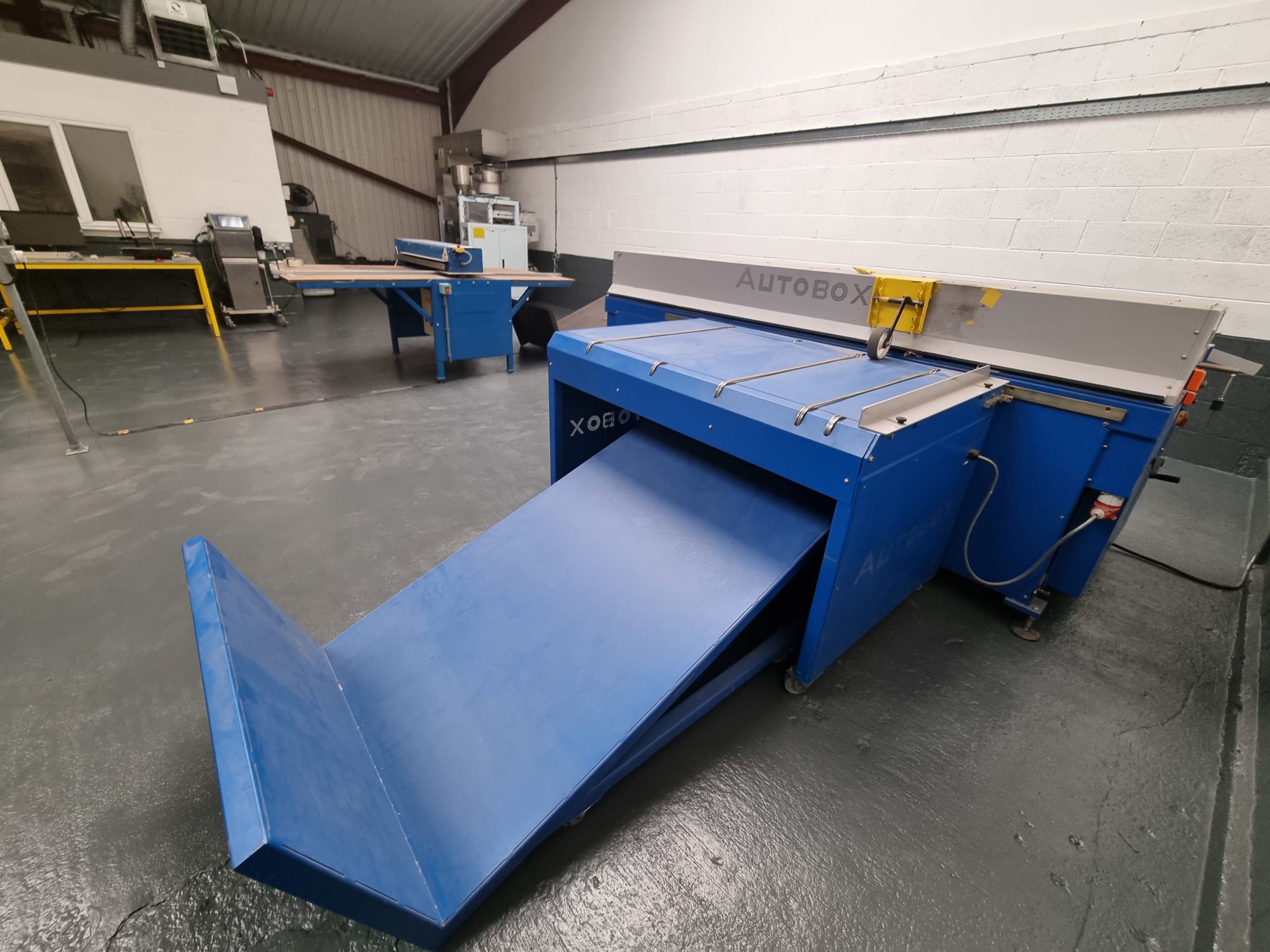
With the increase of the public shopping online throughout the pandemic came the need for increased stock levels being ordered and stored. There is currently a delay in the goods being shipped from the supplier to the UK due to such high demand.
In turn, this creates a knock-on effect as we are finding that when the goods have been received at the docks, there is a huge backlog of containers that need to be booked in for delivery.
Through the peak of backlog, we were seeing up to 5 containers being unloaded by the warehouse team a day, and over 15 a week.
This meant that we had to respond to the sudden increase in stock and expand our current warehouse storage capacity by 35,000 Sqft. This now takes our total up to 28 warehouse units up and down our Kings Cliffe site that we prepared with racking prior to and during the stock arrival. Of course, these units filled up very quickly, so we had to adapt to picking and packing at nearly full capacity, but still offer the service our clients expect of us.
A customer of ours has a large catalogue of items they sell, such as children’s play kitchens and dolls houses. Then throughout the summer months, they sell outdoor furniture such as fire pits, tables and chair sets and water fountains.
As you can probably guess, this type of stock is quite bulky and difficult to fit more than four in one location and to think we have roughly 240 units per container, all ranging from different sizes, space soon fills up. We adapted to this by working around the clock to get the warehouse up to standard and having warehouse team members working extra hours to get all the tasks done.
We integrate with a number of different systems.
Get in touch to find out how we can help.