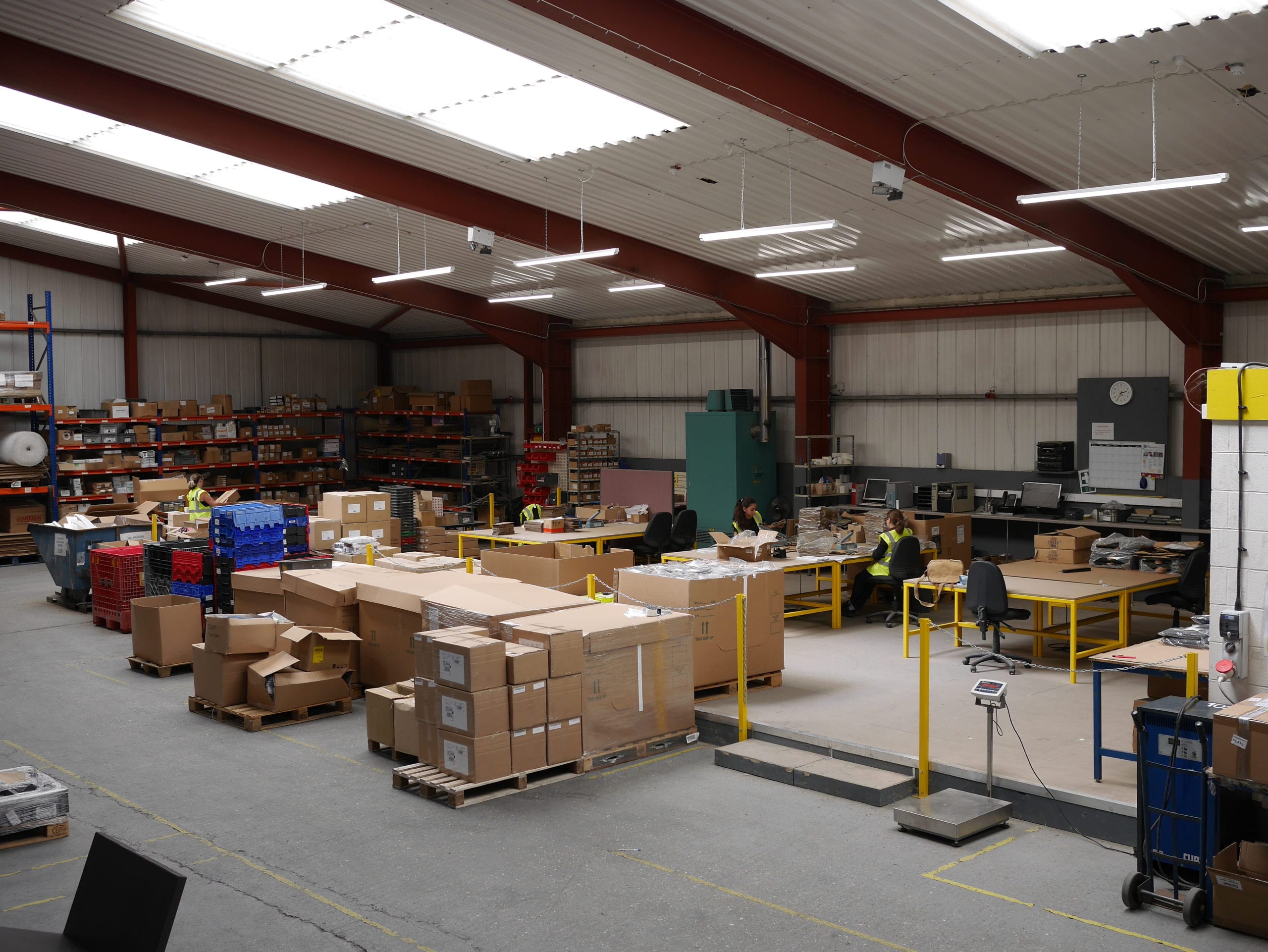
DC is short for Distribution Centre; this means the team specialise in large orders specifically for shipping into Distribution Centres such as Shop Direct, John Lewis and many other major retailer companies. The team is specially trained in the different rules and regulations of the various Distribution Centres.
A DC process can range from needing to book a delivery to get a specific date, time and reference number to having to use spreadsheets to create specialised labels ensuring every letter and number is correct on every product and pallet. Some DC’s will reject a delivery if a product is even 1mm overhang on a pallet or a label is in the incorrect position.
If a delivery is rejected, fines can be anywhere from £500 to £1000, or at worse the customer can lose their contract. Most DC orders have a timed delivery which is provided once we have emailed with a booking request. All shipments including the pallet and the products must be in perfect condition, which includes the wrapping of the pallet, labels positioned in the top left-hand corner (not at different angles) and all the respective DC’s requirements.
Some retailers also require similar processes to be carried out just the same as a Distribution Centre, this means that bookings must be made first, they may only take EURO or standard pallets, and they require certain labels to be placed in certain areas of cartons etc.
Companies are searching for efficient distribution methods that enable broad product assortment, a lower level of inventories, shorter customer order fulfilment and lower transportation costs to achieve a more efficient procurement process – plus an improved level of customer service.
As a result, DCs are balancing inventory costs against tight domestic transportation capacity, rising freight rates and volatile energy prices. An adverse financial impact has occurred due to huge inventory versus transportation trade-offs in time and cost that are taking place in many companies as supply chain strategies are being challenged.
Here at Bray Solutions, we also specialise in Dangerous Goods and the specific requirements for this sector. The DC Team handles this and must follow the exact rules and regulations to make sure everything is in order, and every box is ticked. These usually are Sea or Air Freight which are sent anywhere in the world, so far, we have sent orders as far as the USA, Canada, Australia and Saudi Arabia.
The Dangerous goods regulations are published to provide procedures for a shipper and operator by which articles and substances with hazardous properties are transported safely by air on all commercial air transport. Articles and substances having hazardous properties which, if uncontrolled, could adversely affect the safety of the passengers, crew, and/or aircraft on which they are being carried. Experience with other forms of transportation show such articles and substances can be transported safely provided they are properly packed, and the quantities in each package were properly limited. If you want to transport dangerous goods, there are rules on how to pack and label them and the training your staff must have. Dangerous goods must be packaged and labelled appropriately. Here at Bray Solutions, we specialise in this field, and our Projects and Health & Safety Manager Adam has certification in being CAA registered in Dangerous Goods by air. Our DC team is fully trained in the regulations of packing and labelling.
We provide dangerous goods service for one of our customers who ship perfume around the world. This is due to Perfume being flammable, and as such poses a risk should the perfume bottle break and leak perfume. It could cause a hazard shipping by air or shipping by road which is why dangerous goods procedures must be followed to ensure this does not occur.
We integrate with a number of different systems.
Get in touch to find out how we can help.